Does the drink vending machine have anti-microbial surfaces to ensure hygiene? | MAKMIK Guide
- Does the Drink Vending Machine Have Anti-Microbial Surfaces to Ensure Hygiene?
- What Are Anti-Microbial Surfaces in Vending Machines?
- Adoption of Anti-Microbial Technology in Drink Vending Machines
- Benefits of Anti-Microbial Surfaces for Vending Operators
- Limitations and Professional Considerations
- What Should Operators and Buyers Do?
Does the Drink Vending Machine Have Anti-Microbial Surfaces to Ensure Hygiene?
Drink vending machine operators face rising concerns about hygiene and surface safety. With high-touch areas on vending machines, professionals must ensure anti-microbial protection to meet user expectations and reduce contamination risks. Here, we answer common industry queries with proven facts about anti-microbial solutions.
What Are Anti-Microbial Surfaces in Vending Machines?
- Definition:
Anti-microbial surfaces incorporate materials or coatings that actively inhibit the growth of bacteria, fungi, and some viruses on machine exteriors. - Purpose:
Designed to minimize microbial load and cross-contamination, especially in high-use environments such as offices, hospitals, and public spaces. - Industry Standards:
ISO 22196 specifies test methods to assess anti-microbial activity on plastics and other non-porous surfaces used in vending machines.
(https://www.iso.org/standard/54431.html)
Adoption of Anti-Microbial Technology in Drink Vending Machines
- Recent Trends:
Since the COVID-19 pandemic, many leading vending machine manufacturers are integrating anti-microbial solutions into their machine designs. - Application:
Common touchpoints such as buttons, touchscreens, and dispensing areas are prime targets for anti-microbial coatings. - Product Examples:
- Some global brands now feature anti-microbial films or powder-coated surfaces.
- Retro-fitting kits are available for older machine models. (https://www.vendingtimes.com)
Benefits of Anti-Microbial Surfaces for Vending Operators
- Enhanced Hygiene:
Reduces surface contamination, promoting a safer vending experience for users and staff. - Compliance:
Eases regulatory compliance for companies operating in sectors with strict hygiene standards (healthcare, education, etc.). - Brand Trust:
Demonstrates proactive health and safety measures, boosting consumer confidence and machine usage rates.
Limitations and Professional Considerations
- Surface Efficacy:
Anti-microbial coatings are effective against microorganisms, but not a replacement for routine cleaning protocols. - Durability:
Some anti-microbial films or coatings may degrade over time or with intensive cleaning—plan for periodic inspection and replacement. - Cost Factors:
Upgrading to anti-microbial vending machine surfaces may involve higher upfront costs, but long-term savings may be realized through fewer contamination incidents.
What Should Operators and Buyers Do?
- Evaluation:
Review vendor specifications for anti-microbial accreditation (e.g., ISO-certified materials). - Maintenance:
Pair anti-microbial surfaces with comprehensive cleaning schedules for maximum hygiene. - User Education:
Communicate surface benefits to end users to reinforce positive machine interactions and confidence.
Summary Table
Feature | Benefit | Consideration |
---|---|---|
Anti-microbial Coating | Limits microbial growth | Needs regular inspection |
Touchpoint Protection | Safer user experience | Not a sole hygiene solution |
Compliance | Aids in meeting hygiene standards | May increase machine cost |
Brand Perception | Enhances user trust | Requires ongoing communication |
For more on anti-microbial solutions in vending machines, industry best practices, or to request a consultation, contact MAKMIK, your professional vending machine partner.
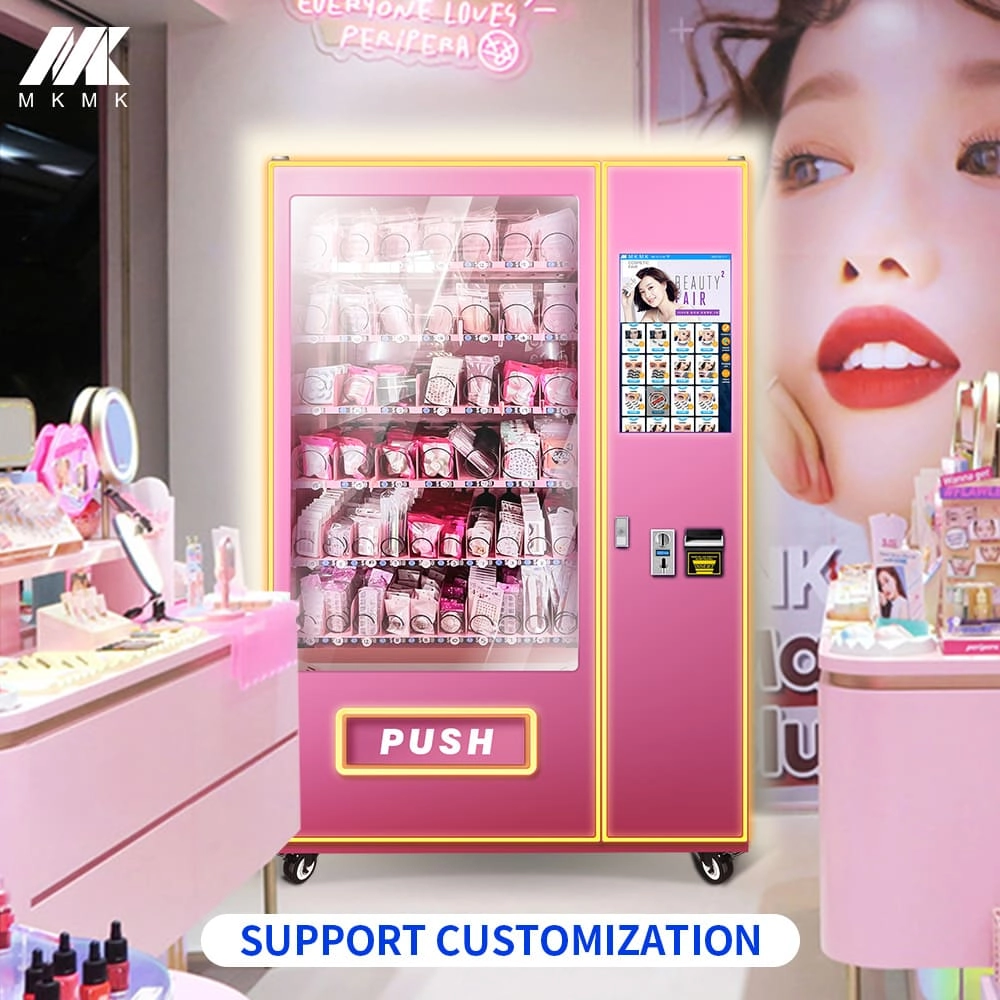
Top 10 Best-Selling Products in Smart Beauty Vending Machines
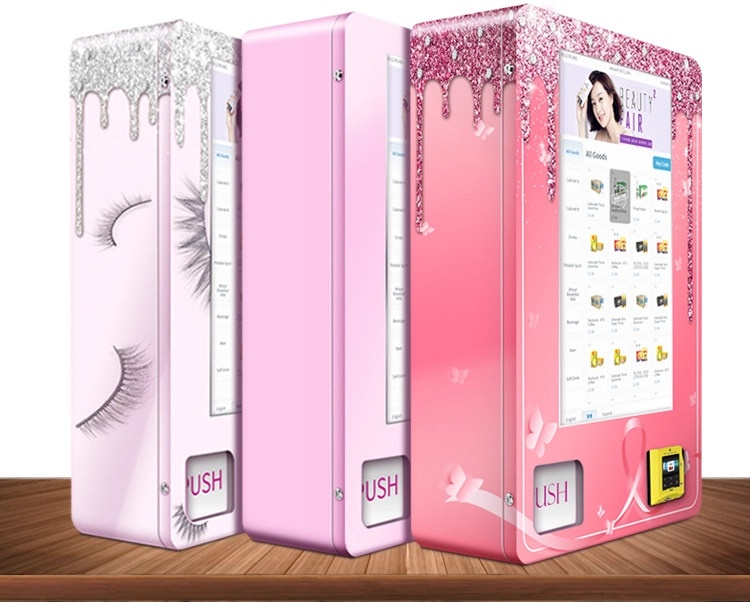
Smart Beauty Vending Machine Trends in 2025: What You Need to Know
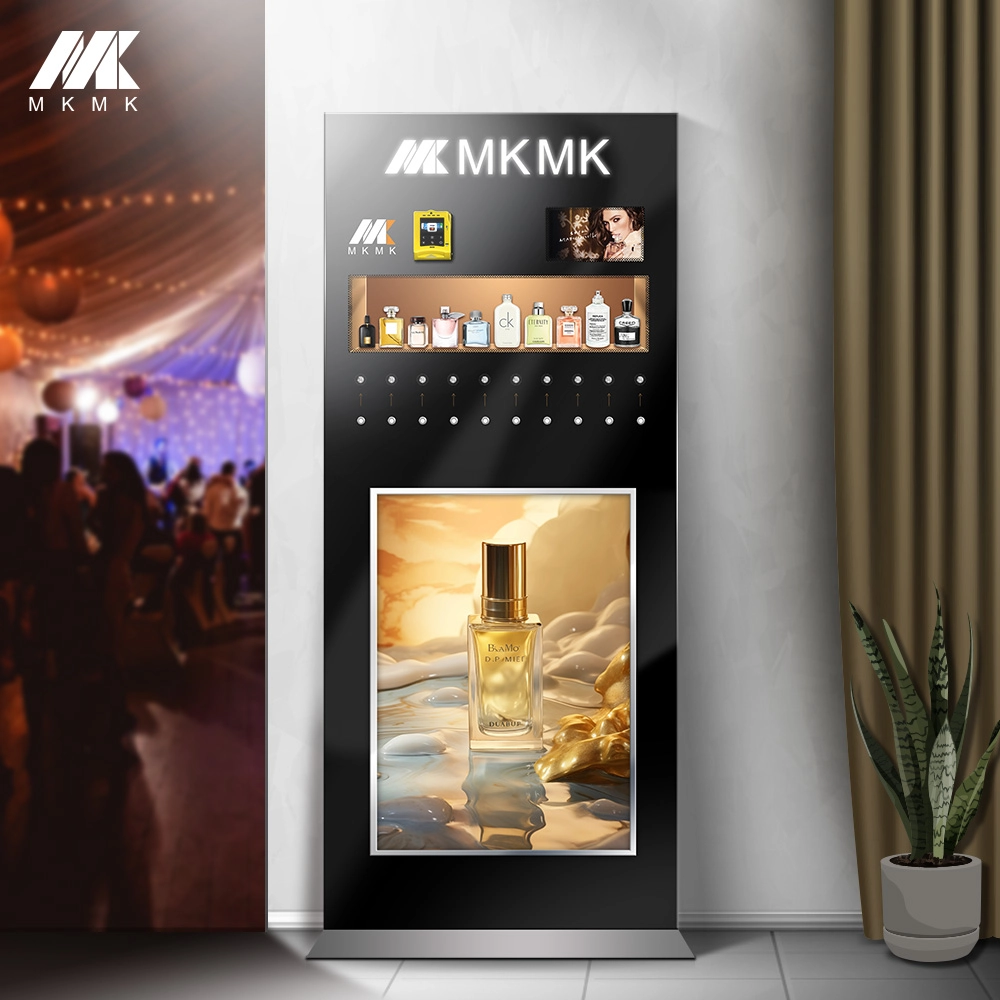
How to Choose a Perfume Vending Machine – Key Factors to Consider
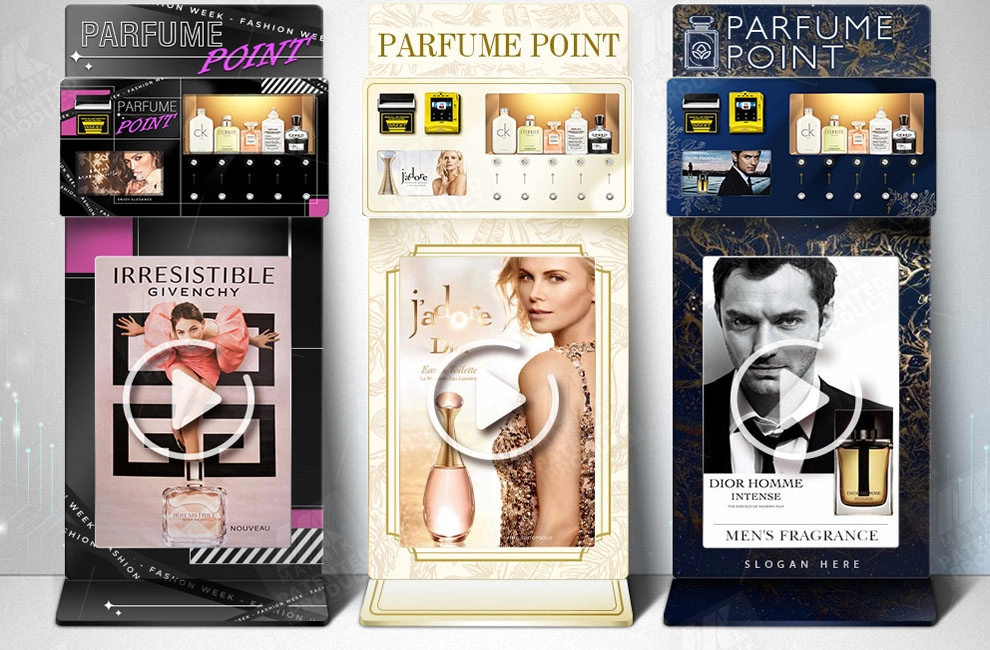
Top 10 Perfume Vending Machine Supplier Brands
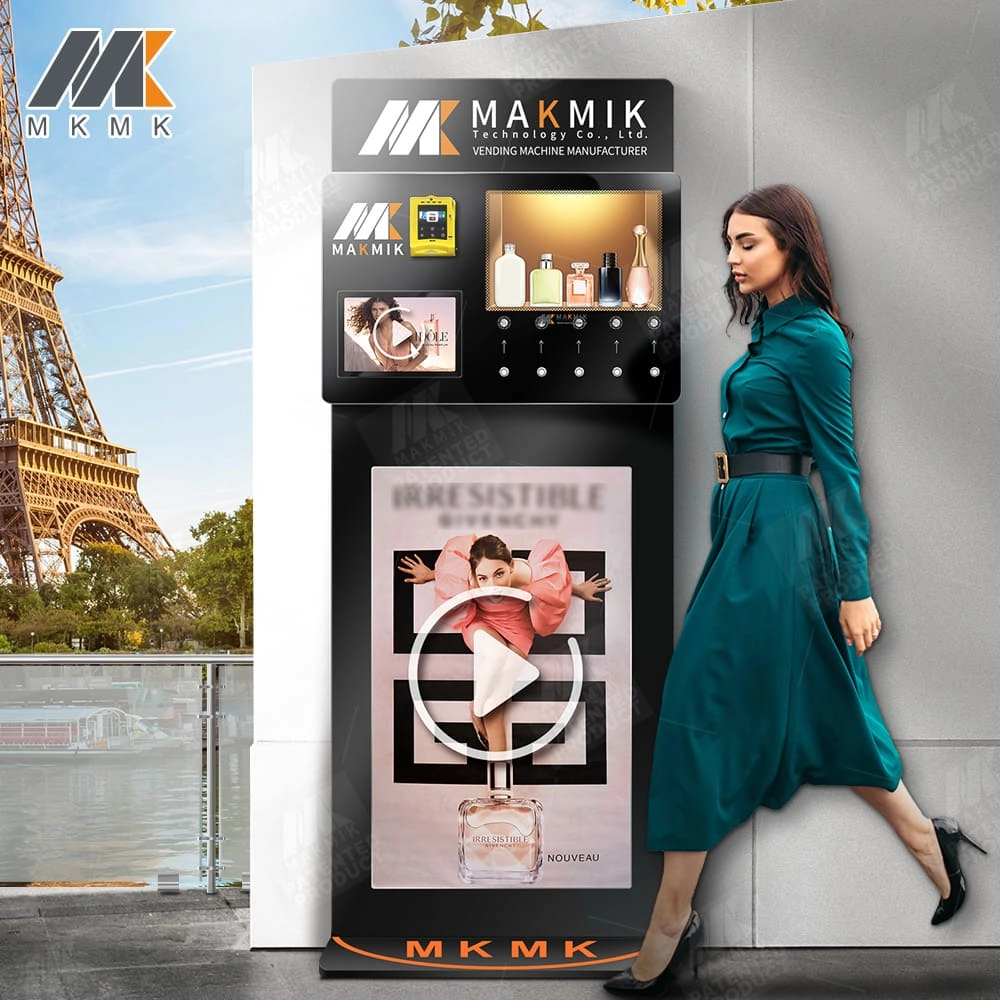
The Ultimate Perfume Vending Machine Maintenance Guide
FAQ
Are your vending machines energy-efficient?
Yes, our vending machines are designed with energy-efficient technologies to reduce power consumption and minimize environmental impact.
What payment options do your vending machines support?
Our vending machines support various payment methods, including cash, credit/debit cards, mobile payments, and contactless payments.
How can I monitor and manage my vending machines remotely?
Our vending machines come with advanced telemetry systems that allow remote monitoring and management through a web-based platform or mobile app.
Do you offer warranties on your vending machines?
Yes, we provide warranties on all our vending machines, covering parts and labor for a specified period to ensure peace of mind for our clients.
Can your vending machines be customized?
Yes, we offer customization options to meet specific client requirements, including branding, product selection, and payment systems.
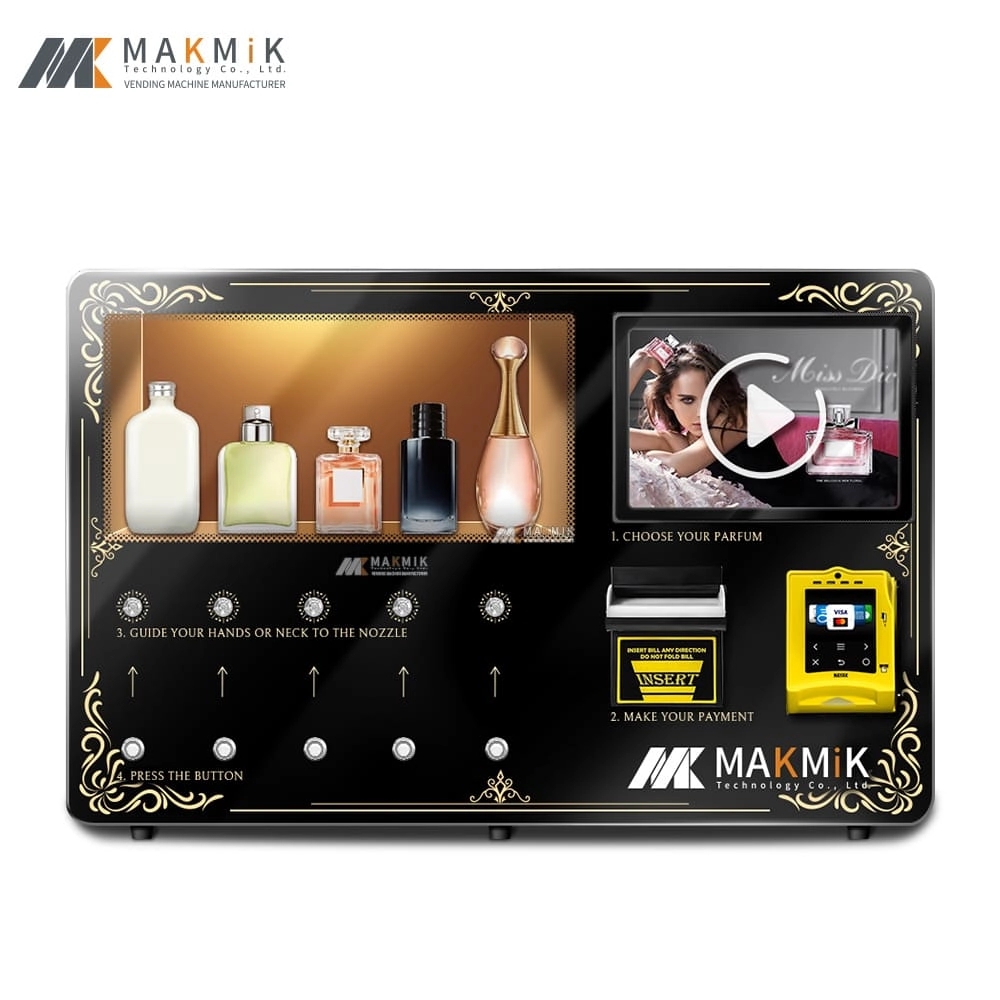
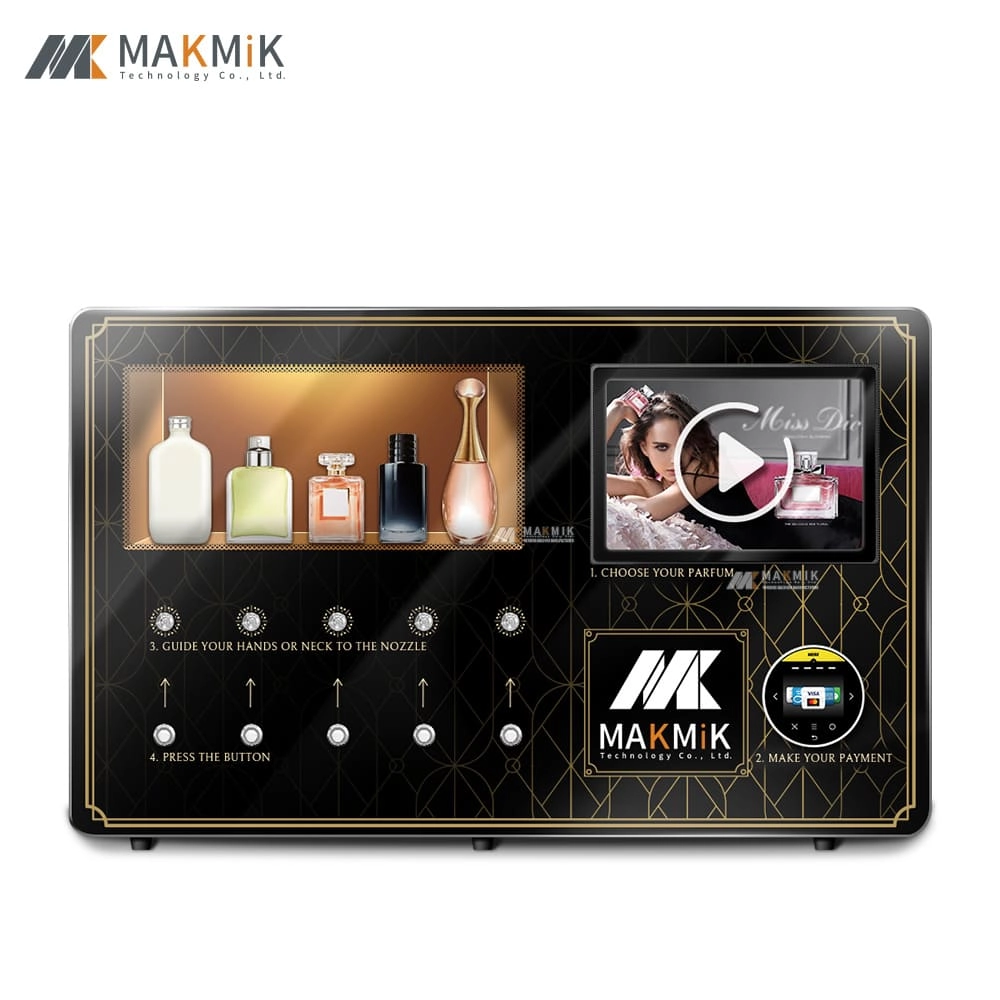
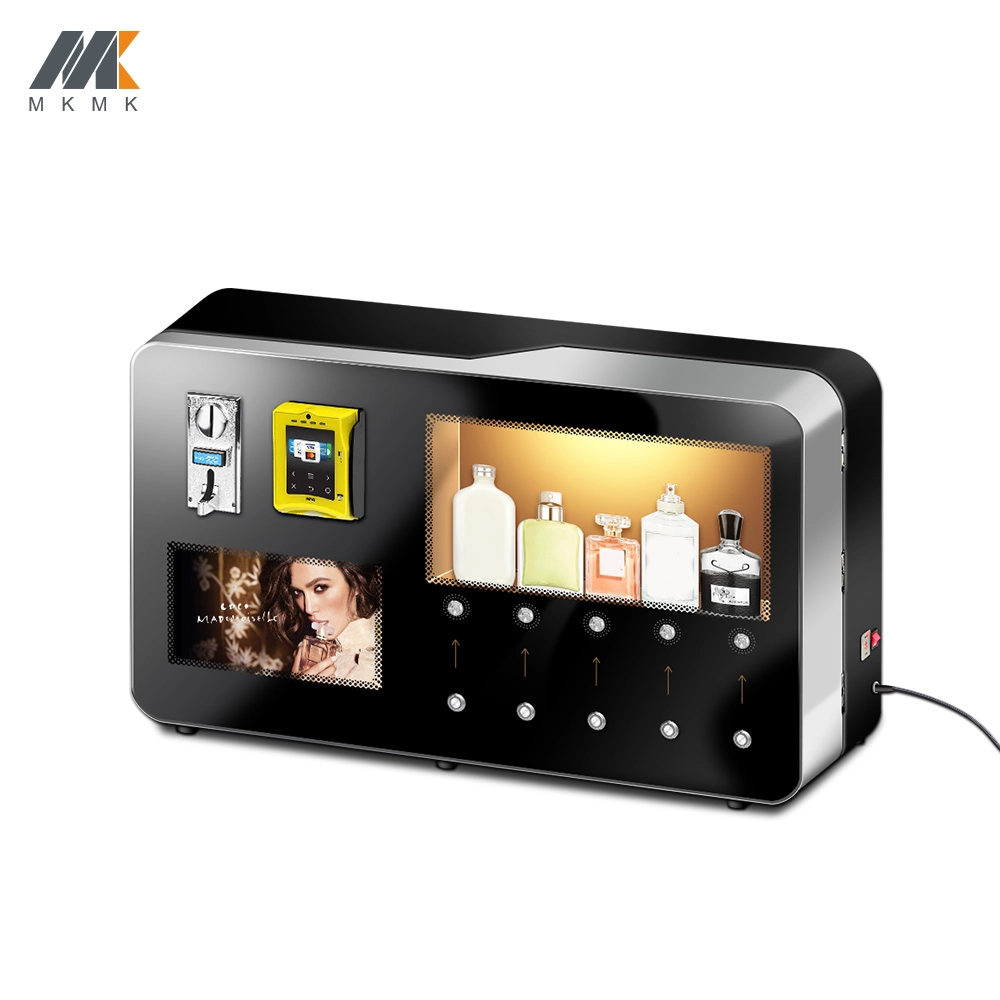
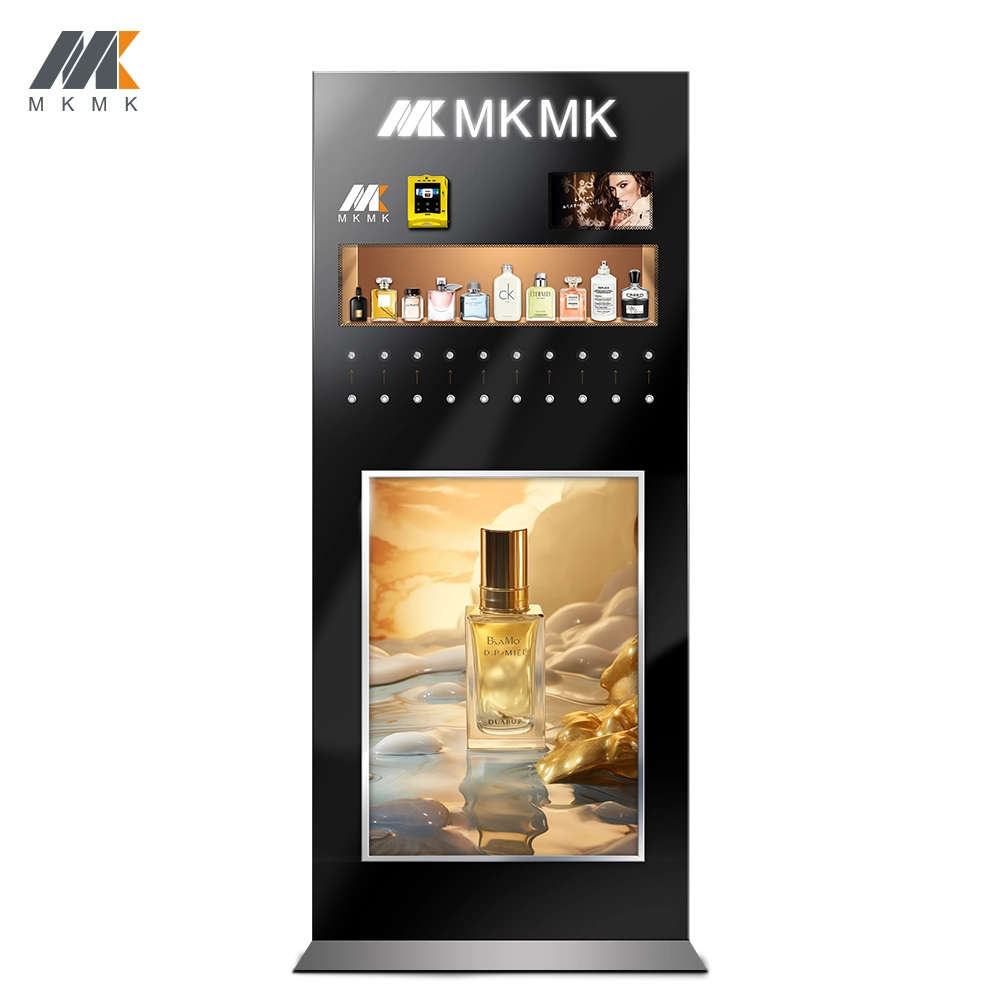
Send my request
Connect with us to schedule a consultation, request samples, or arrange a site visit to see our facilities and capabilities firsthand.
Reach out to us via phone, email, or through the contact form below, and we'll get back to you promptly within 24 hours.
© 2025 MAKMIK | All Rights Reserved.